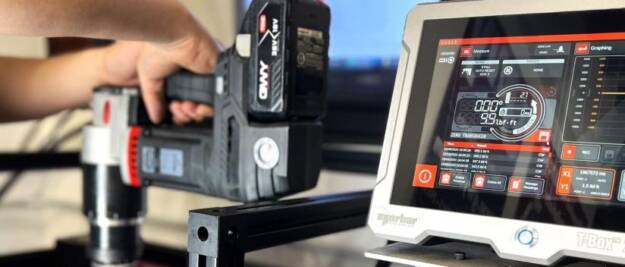
When it comes to tightening bolts with precision, a torque wrench is the tool you trust to get the job done right. But even the most reliable tools require regular attention to stay accurate.
Understanding when and why to calibrate your torque wrench isn’t just a matter of routine maintenance — it’s a crucial step in ensuring your work meets the highest standards of safety and quality. Whether you’re a seasoned professional or a dedicated DIY enthusiast, knowing how often to calibrate your torque wrench can save you time, money and frustration down the line.
What Is Torque Wrench Calibration?
Torque wrench calibration is the process of verifying and adjusting a torque wrench to ensure it delivers accurate and consistent torque readings. The process involves comparing the tool’s output against a known standard and making adjustments if necessary to match precise specifications.
Calibration ensures that a torque wrench remains reliable and effective, which is essential for projects where accurate bolt tensioning directly impacts structural integrity and safety. For professionals and DIYers alike, regular calibration is a critical step in maintaining the performance and longevity of their tools.
Why Is Regular Calibration Necessary?
Even the most durable torque wrenches can drift out of specification over time due to frequent use, mechanical shock or environmental factors. This is why regular calibration is essential.
When a torque wrench provides inaccurate readings, it compromises the quality and safety of a project. Under-tightening can leave connections loose and vulnerable to failure, while over-tightening can damage components and reduce their lifespan. In industries like construction and manufacturing, inaccurate torque can lead to costly rework or even hazardous situations.
Regular calibration ensures a torque wrench continues to deliver reliable, precise performance, giving users the confidence that every fastener is properly tightened according to specification.
How Often Do You Need to Calibrate a Torque Wrench?
How often you need to calibrate a torque wrench depends on how frequently it’s used and the environment in which it operates.
Industry standards generally recommend calibrating a torque wrench at least once a year or every 5,000 cycles — whichever comes first. However, tools exposed to harsh conditions, such as extreme temperatures, heavy-duty applications or frequent transport, may require more frequent calibration to maintain accuracy.
For professionals who rely on precise torque application, following a time-based (once a year) or usage-based (every X cycles) schedule ensures consistent performance.Those who use their torque wrenches less frequently may still benefit from annual calibration to account for potential changes in accuracy caused by storage conditions or occasional impacts. Staying on top of your tool calibration prevents potential issues before they affect critical projects.
Factors That Affect Calibration Frequency
Several factors influence how often a torque wrench needs calibration, with environment and intensity of use being the most significant.
- Intensity of use: Tools used daily or in high-torque applications are more likely to drift out of calibration than those used occasionally. Repeated heavy use, especially in industrial or construction settings, accelerates wear on internal components.
- Environmental conditions: Exposure to dirt, moisture, extreme temperatures or corrosive substances can compromise a torque wrench’s accuracy. Even storage conditions matter — tools left unused for long periods or stored improperly may lose accuracy over time.
- Transportation: Torque wrenches that are frequently moved between job sites or tossed into tool bags without proper protection are at higher risk of damage or calibration loss.
Torque wrench users need to monitor these factors and adjust calibration schedules accordingly to ensure reliable, accurate performance when it matters most.
Best Practices for Torque Wrench Maintenance and Care
Keeping a torque wrench in peak condition requires more than just regular calibration. Proper maintenance and handling can significantly extend the tool’s accuracy and lifespan. Follow these best practices to keep your torque wrenches ready for the next project:
- Store your wrench properly: Always store your torque wrench in a protective case when not in use. Avoid damp, dusty or extremely hot environments that can affect the tool’s performance.
- Avoid dropping or mishandling: Mechanical shocks from accidental drops or rough handling can alter the wrench’s calibration. Handle with care and transport it securely between job sites — use a tool lanyard if necessary.
- Use the wrench correctly: Follow manufacturer guidelines to avoid overloading or applying force incorrectly. Misuse can quickly throw a torque wrench out of calibration.
- Clean regularly: Keep the wrench clean and free of debris, especially around the head and mechanism. Lubricate parts as recommended by the manufacturer.
- Calibrate annually: Even with proper care, torque wrenches should be calibrated at least once a year or every 5,000 cycles to maintain accuracy and reliability.
If you’re wondering how to calibrate a torque wrench, the simplest answer is to trust the experts. GWY provides fast, efficient and reliable in-house calibration services performed by a team of skilled technicians. Reach out to us today to keep your torque wrenches performing with absolute accuracy and confidence.
Frequently Asked Questions
How do I know my torque wrench needs calibration?
Signs that your torque wrench needs calibration include inconsistent or inaccurate torque readings and noticeable wear on the tool — or, if it has been dropped or exposed to harsh conditions. If you find yourself over-tightening or under-tightening fasteners despite following proper procedures, it’s likely time for calibration. Following a regular calibration schedule — such as once a year or every 5,000 cycles — helps ensure accuracy before problems arise.
What happens if a torque wrench isn’t calibrated?
An uncalibrated torque wrench delivers inaccurate torque readings, which can lead to serious issues. Under-tightening can cause fasteners to come loose, jeopardizing the structural integrity of a project. Over-tightening can damage bolts, threads or connected components, reducing their durability and increasing the risk of costly rework. In critical applications, a poorly calibrated wrench can compromise safety and lead to equipment failure or structural damage.