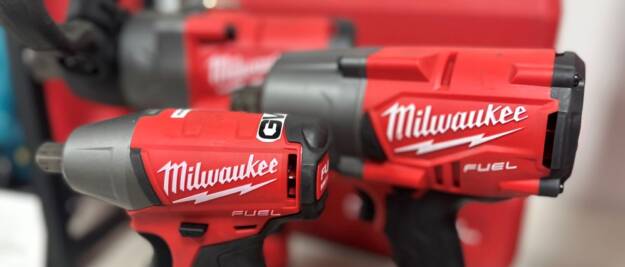
No matter what kind of job you’re tackling, the tool in your hand makes a difference. From fine-tuning machinery in a garage to installing structural bolts on a steel frame, the right torque wrench doesn’t just help you get the job done — it impacts how fast you work, how consistently you hit spec and how safe your setup stays over time.
As battery-powered impact wrenches grow in popularity for their convenience and power, manual torque wrenches remain a dependable standard, trusted for their accuracy and control. Understanding the strengths and limitations of each is key to selecting the tool that fits your work style and the demands of the job.
Battery-Powered Impact Wrenches: Features, Benefits and Use Cases
Cordless, battery-powered impact wrenches are electric tools designed to deliver fast, powerful torque without the need for manual force or an external air supply. Using a rotating mass and hammering mechanism, they generate bursts of high torque, which is ideal for loosening and tightening bolts quickly and efficiently.
These wrenches excel in applications that demand speed and mobility. Their high torque output enables the user to tackle stubborn fasteners with ease, while the cordless design means no cords or compressors to slow you down. This combination makes them a favorite for automotive repairs, steel construction and other heavy-duty jobs where every second counts.
Another benefit is that impact wrenches do not require calibration in the same way that torque wrenches do because they’re not designed to deliver a specific, repeatable torque value. Instead, impact wrenches are torque-generating tools, meant for quickly loosening or tightening fasteners with power, not precision. While some models include torque control features or adjustable settings, these are approximate and not substitutes for calibration.
That said, routine maintenance is critical:
- Check for wear on internal components like hammer mechanisms and anvils
- Inspect battery performance and tool housing
- Use a calibrated torque wrench to verify final tightness if torque accuracy matters
If your application requires verified torque values such as in structural steel, bridge work or flange assemblies, always follow up with a calibrated torque wrench. GWY recommends pairing impact tools with precision-calibrated torque wrenches to ensure compliance and performance.
For professionals and DIYers alike, cordless impact wrenches offer a balance of power and convenience that few other tools match. Milwaukee’s line of square drive torque wrenches (the 2758-22CT, 2767-22, 2864-22 and 2867-22) is popular for its durability, precision and portability, providing job-ready performance across a wide range of applications.
Manual Wrenches: Strengths, Limitations and Ideal Applications
Manual torque wrenches are hand-operated tools used to apply torque to fasteners without the need for electricity or compressed air. This category includes tools like click-type torque wrenches, beam-style torque wrenches and standard socket wrenches. They rely entirely on the user’s control, offering a level of precision that’s ideal for tasks where accuracy is critical.
One of the biggest advantages of manual torque wrenches is their independence from any power source. They’re easy to store, transport and use in tight or remote environments where electric tools aren’t practical. These tools are also typically more budget-friendly, making them a go-to option for occasional users or anyone looking for a reliable backup to powered tools.
Unlike impact wrenches, manual torque wrenches absolutely need to be calibrated, and regularly. Over time, mechanical components can drift out of spec due to wear, impact or environmental conditions. If a manual torque wrench isn’t properly calibrated, it can apply too much or too little torque, risking structural failure, safety issues or failed inspections.
Calibrate your manual torque wrench at least once a year or after 5,000 cycles, whichever comes first. Also recalibrate if the wrench is dropped or exposed to harsh conditions, or before using in critical applications. GWY offers in-house calibration services using equipment rated up to 36,000 ft-lb, ensuring your tool is accurate and ready for the next job.
When exact torque values are essential — such as in machinery calibration, flange bolting or light industrial maintenance — a well-calibrated manual torque wrench is hard to beat. Popular models like the Norbar Pro800 and the TONE T4MF100 are trusted across industries for their repeatable accuracy and sturdy design, helping ensure every fastener meets spec without over-tightening.
Key Differences for Easy Comparison
Choosing between a manual and battery-powered impact wrench often comes down to balancing performance needs with budget and project demands. Here’s how the two compare across core decision-making factors:
Battery-Powered Impact Wrench | Manual Wrench | |
Power | Delivers significantly higher torque for heavy-duty applications | Relies on user strength; suited for lighter tasks |
Efficiency | Speeds up work with fast, consistent torque delivery | Requires more time and effort to reach desired torque |
Cost | Higher upfront investment, long-term value in time saved | Lower cost initially; ideal for infrequent use |
Maintenance | Needs battery management and occasional motor service | Minimal upkeep; simple design means fewer failure points. Requires calibration! |
Usability | Easy to operate but heavier, bulkier and noisier | Lightweight, precise, better control for sensitive tasks |
Which One Should You Choose?
Both tools have a place on the job site or in the shop. The right choice depends on how often you use it, what you’re tightening and how much precision you need.
If your work demands high torque and fast-paced performance, a battery-powered impact wrench delivers the power and speed to keep up. It’s the clear choice for professionals in construction, automotive and industrial settings who need muscle without being tied to cords or compressors.
If you’re looking for a budget-friendly option or need absolute control over torque settings, a manual wrench offers unmatched precision. It’s especially well-suited for occasional users, smaller tasks and jobs where over-torquing is a concern.
For those who want flexibility across a range of applications, there’s value in having both. Use a cordless impact wrench to break loose fasteners or power through installations, then switch to a manual torque wrench to finish to spec. Together, they give you speed and accuracy, without compromising on job quality.
If you’re ready to upgrade your toolkit, GWY carries a full line of high-performance cordless impact wrenches built for power, durability and precision. Whether you’re tackling heavy-duty installs or looking for a reliable jobsite companion, our curated selection is built to perform. Explore our top-rated models and find the right fit for your work.
Purchase or Rent:
FAQs
Are cordless impact wrenches better than manual wrenches?
Not necessarily — they’re just better for certain tasks. Cordless, battery-powered impact wrenches excel when you need speed and high torque, especially for repetitive or heavy-duty applications. Manual wrenches, on the other hand, are more precise and better suited for tasks where accuracy is critical. The best choice depends on your application, workload and need for portability or control.
Can a cordless impact wrench replace a torque wrench?
No. While battery-powered impact wrenches can quickly tighten bolts, they don’t provide the accuracy required for achieving a specific torque value. For any job that requires verified torque settings, such as structural bolting or engine work, a properly calibrated torque wrench is essential.
What size impact wrench do I need?
It depends on the type of fasteners and materials you’re working with. A 1/2″ drive is the most common for general-purpose use, offering a balance of power and versatility. For structural or heavy industrial jobs, a 3/4″ or 1″ drive may be more appropriate to handle larger bolts and higher torque demands.